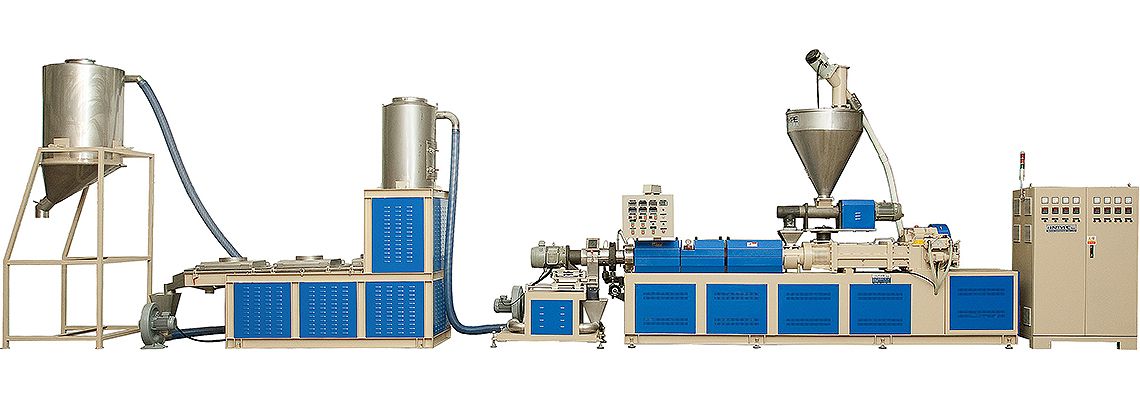
Die-Face Cutter Type Recycling Machine
TDP
The Die-Face Cutter Type Recycling Machine is engineered for efficient recycling of various plastic materials like PVC and PE. Designed to meet the high demands of plastic manufacturing plants, this machine integrates advanced technology for high-quality pellet production with reduced energy consumption. Below, we highlight its essential features, each contributing to enhanced efficiency, high-quality output, and optimized recycling processes.
Characteristic of the Machine
- Patented Screw Design for Low-Temperature Mixing:The unique screw design allows for low-temperature mixing and pelletizing of plastics such as PVC and PE, minimizing energy use while preserving the material's original properties. This feature is ideal for recycling operations focused on maintaining plastic quality and reducing costs.
- Complete Plant Solutions for Plastic Recycling:We offer comprehensive support from design through to manufacturing and installation, providing a complete plant solution tailored to plastic recycling facilities. This turnkey service ensures a smooth and efficient setup, ideal for manufacturers looking to optimize their recycling operations.
- Advanced Vacuum-Assisted Degassing System:Our vacuum degassing system effectively removes moisture, waste gases, and dust, resulting in high-density and high-quality plastic pellets. This system is critical for ensuring stable, high-output production, making it a preferred choice for plants producing premium recycled plastic pellets.
- High-Efficiency Transmission System with Heavy-Duty Gearbox:Featuring a straight transmission design with high-torque output and forced lubrication, the system guarantees stability, low noise, and exceptional performance. This setup ensures higher output even under high-speed operations, maximizing productivity for intensive recycling applications.
- Smart PLC Control System for Enhanced Automation:Equipped with a PLC control system, this recycling machine supports both fully and semi-automatic operations. This flexibility is beneficial for various plastic pelletizing applications, simplifying operational processes and improving production efficiency.
- Customizable Design for Specific Production Needs:Our Die-Face Cutter Type Recycling Machine can be customized based on specific customer requirements. From screw design to transmission settings, every component can be tailored, ensuring optimal performance for unique plastic recycling challenges.
Optional Equipment
- Sound-Absorbing Type Strong Crusher / Feeder / Jumbo Bag Storage Tank.
- Washing & Cleaning System.
- Pulverize Machine.
- High Speed Mixer & High Speed Cool Churning M/C.
- Feeding & Storage System.
- Raw Material Conveying System.
- Dosing System.
- Air Compressor.
- Chiller Cooling System.
- Storage System.
- Vent System.
- Vibration Unit.
- Bagging & Packaging & Weighing System.
- Material Convey System.
Digital control of components and actual monitoring of production processes and quality, which also means that we are always close to the needs of customers.
Die-Face Cutter Type Recycling Machine | Plastic Profile Extrusion Solutions | Intype
Located in Taiwan since 1963, Intype Enterprise Co., Ltd. is a high efficiency plastic extrusion machines manufacturer. Their main plastic extrusion machines include, Die-Face Cutter Type Recycling Machine, sustainable plastic extrusions, continuous bead foam machines, supercritical reaction pelletizers, medical tube extrusion lines and profile extrusion machinery. Their offerings also encompass medical tube extrusion lines and profile extrusion systems. Intype is committed to innovation, quality, and environmental sustainability, focusing on efficient, eco-friendly technologies.
Discover Intype's advanced Plastic Extrusion Machines, a blend of innovation and 60 years of expertise. Specializing in TPE Wood-like Profiles, Continuous Bead Foam, and Supercritical Reaction Pelletizing, our machines are designed for efficiency and sustainability. Ideal for B2B buyers in the plastic extrusion industry, our products range from Medical Tube Extrusion Lines to Profile Extrusion and Recycling Solutions. Intype machines are synonymous with quality, precision, and eco-friendliness, ensuring optimal performance and environmental responsibility. Join the forefront of plastic extrusion technology with Intype's reliable and advanced solutions.
Intype has been providing customers with high efficiency plastic extrusion machines since 1963, with both advanced technology and 50 years of experience, Intype ensures that each customer's requirements are met.